[ Instrument network instrument research and development ] Use renewable electricity to drive CO2 electrocatalytic reduction to high value-added chemical fuels such as methanol and formic acid. While solving excessive CO2 emissions, it can also realize the direct conversion of intermittent electrical energy to chemical energy, and control carbon. It is of great significance to balance and optimize the energy consumption structure. Because the C = O double bond in the CO2 molecule is stable, the energy required for electrocatalytic CO2 reduction (CO2RR) is high. Therefore, the development of efficient catalysts to improve the catalytic efficiency of reactions is the focus and difficulty of CO2RR research.
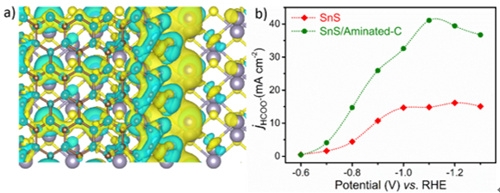
In a chemical reaction, a substance that can change the chemical reaction rate (increase or decrease) of a reactant without changing the chemical equilibrium, and whose quality and chemical properties have not changed before and after the chemical reaction is called a catalyst (a solid catalyst is also called a catalyst). According to statistics, more than 90% of industrial processes use catalysts, such as chemical, petrochemical, biochemical, and environmental protection. There are many types of catalysts, which can be divided into liquid catalysts and solid catalysts according to the state; homogeneous catalysts and heterogeneous catalysts according to the phase state of the reaction system. The homogeneous catalysts include acid, alkali, soluble transition metal compounds, and peroxide catalysts. The catalyst occupies an extremely important position in the modern chemical industry. For example, iron catalysts are used in the production of ammonia, vanadium catalysts are used in the production of sulfuric acid, the polymerization of ethylene and the production of butadiene rubber are used in the production of three major synthetic materials. Different catalysts are used. .
In the past ten years, various catalysts have been developed for the research of CO2RR, and some progress has been made on key scientific issues such as increasing product selectivity and reducing overpotential, but the reaction current density and catalytic yield of CO2RR are still low. , Can not further meet the needs of industrial applications.
Electrocatalysis is a catalytic action that accelerates the charge transfer reaction at the electrode and electrolyte interfaces. The scope of electrode catalysts is limited to electrical materials such as metals and semiconductors. Electrocatalysis has been studied more on framework nickel, nickel boride, tungsten carbide, sodium tungsten bronze, spinel and tungsten ore semiconductor oxides, and various metal compounds and phthalocyanine catalysts. It is mainly used in the electrocatalytic treatment of organic sewage; the electrocatalytic degradation of chromium-containing wastewater; the electrolytic desulfurization of flue gas and raw coal; the electrocatalytic removal of NOx and S02 simultaneously; the electrolytic reduction of carbon dioxide and nitrogen.
The Research Group of Environmentally Friendly Catalytic Process of Qingdao Institute of Bioenergy and Process of Chinese Academy of Sciences has carried out a lot of research work on the development of high-efficiency electrocatalysts. Recently, based on previous research work, the research group found that directly coating the amino-functionalized carbon layer can effectively regulate the electronic structure of the non-precious metal catalyst SnS, thereby accelerating the electron conduction efficiency at the electrode interface and enhancing the catalyst's adsorption state. The adsorption capacity of the CO2 molecule and the reaction intermediate OCHO * achieved a significant increase in the reaction current density and catalytic yield. This research work provides a new strategy for improving the catalytic activity of transition metal catalysts.
Source: Qingdao Institute of Bioenergy and Process, Encyclopedia
Engineering Plastics
Engineering Plastics
Engineering plastics are a bunch of plastics that are used most ordinarily in industries because of their enhanced mechanical and thermal properties. They are used mainly in situ of thermoplastic materials instead of thermosetting ones because of the fact that they will be remolded into the specific shape and size whether or not after cooling and settling down. In accordance, to the suitable convention and standards, the definition of engineering plastics (McQuiston, 1980) are: (1) the family of nylon; (2) polycarbonate; (3) polyphenylene oxide; (4) acetal; (5) engineering grade of ABS; (6) polysulphone; and (7) polyphenylene sulphide. Engineering plastics become the fabric of choice for various applications because of their good mechanical, chemical properties, strength, rigidity, self-lubrication, and fire safety. Certain groups of engineering plastics which include polycarbonates and polyamides are useful in industries due to their high resistance to impact and abrasion respectively.
Engineering Plastics,Multi-Functional Engineering Plastics,Thermoforming Plastics,Degradable Plastics
Sunrise Group Corporation , https://www.sunriseindust.com