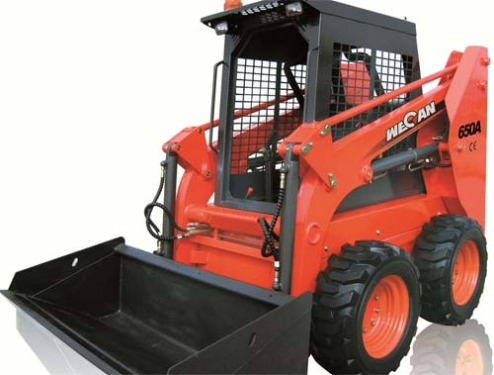
Many ERP and APS software on the market cater to the needs of production plans to manage chaos, claiming that they can help companies to develop a reasonable production plan or feasible scheduling plan. We believe that software is only auxiliary, if the company does not figure out the plan The rules of production, then, no matter how good the software can not rationalize the plan. Businesses must first be familiar with the planning rules, and then make reasonable changes based on the rules.
We have divided the production plan into three levels:
The first floor, scheduling. The process of converting an external order or internal forecast into a production order sheet is to determine at what point in the next planning cycle how many finished products should be produced.
The second floor, scheduling. That is, the process of row production, this step needs to determine the equipment needed at any point in time and the production of various processes according to the output plan of the finished product.
The third level, implementation. That is, feedback on the completion of the production process will form a closed loop for the entire planning process.
The second level of the plan is the focus of the entire process. So how do you plan your schedule according to certain rules? To illustrate with a case. At the end of each month, a company will conduct a unified scheduling of sales orders and production forecasts for the next month. After that, it will conduct additional sporadic scheduling of new sales orders. For such a situation, we first divide the entire schedule. The cycle, see below:
Among them, the first period is the implementation period of the plan. The plan for this period has already reached the workshop, and raw materials and molds are already in place. The plan is not allowed to change unless there is a problem with the plan itself. After the completion of planned production within the implementation period, there will be feedback on the corresponding production completion situation. We can adjust and release the plan for the next implementation period based on the feedback situation. In this way, as time progresses, the execution period will roll forward in a 1-2 day cycle.
The second period is the preparation period of the plan. The plan sheet for this period has already been confirmed to the purchasing department and related preparations for production. If you want to make changes to the plan during this period, you must follow certain rules. For example, if a new order with a close delivery date is inserted into a single order operation, it should first be confirmed to the purchasing department: The raw materials needed for this batch of orders can be purchased on time. If not, there is no point in inserting a single order. Even if it is possible to insert a slip with other production preparation factors, it is also necessary to evaluate whether the extension of other plans caused by the insertion slip is appropriate. At the same time, the period of the production preparation period will continue to shorten as the implementation period advances. When the implementation period is advanced for one week, the preparation period will be rolled forward again for another week. That is, the production plan for the next week will be issued to the procurement and other departments for production preparation. In other words, the production preparation period is rolling for the week.
The last period of the plan is the horizon. During this period, the production plan is for reference only by planners and can be changed at any time without affecting production. There are no other related actions.
In this way, by layering and subdividing phases and following certain rules, the arrangement of production forklifts will be arranged. The entire plan will be clearly structured and clearly defined. Production planners are skilled in mastering such a planning model. The cooperation among various departments will be a good way for the production plan to truly roll up.
Airless Cream Jar,Airless Cream Empty Jar,Acrylic Airless Jar,Skin Care Jar
Shaoxing Dingsheng Plastic Products Co..Ltd. , https://www.dingshengpacking.com